SHIPBUILDING
SPECIAL REPORT: Accelerated Training Program Prepares Students for Shipbuilding Careers
By Allyson Park
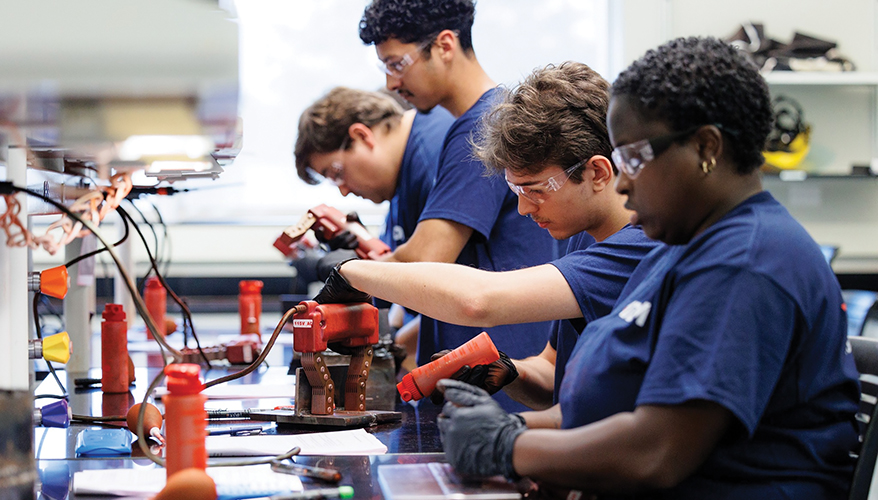
Accelerated Training in Defense Manufacturing photo
This is part 3 of a 5-part special report on the shipbuilding industry.
DANVILLE, Virginia — As the shipbuilding and submarine industrial bases struggle to hire and retain younger workers, the Navy is funding a program to boost their numbers.
The Accelerated Training in Defense Manufacturing, or ATDM, program in Danville, Virginia, is dedicated to addressing the hiring and retention dilemma within shipyards by training a new workforce for shipbuilding, maintenance and repair at a rigorous and expedited pace.
Hiring and retaining quality workers for manual jobs in shipyards — as many workers from the “baby boomer” generation retire — is one of the biggest challenges facing the shipbuilding industrial base, said Jason Wells, ATDM program manager and executive vice president of manufacturing advancement at the Institute for Advanced Learning and Research.
“I think it’s still a manual labor-intense environment,” Wells said in an interview. “With a lot of other industries that are advancing and incorporating technologies that have really shaped or reshaped the landscape of what the old image of manufacturing looked like to a more modern, technology-driven, very clean … very safe environment, … it’s created a really challenging landscape for an old, antiquated shipyard to compete against.”
While the need to evolve with technology permeates the defense industrial base, modernization has not reached the shipyards yet, which can deter potential workers, especially younger ones, Wells said.
The program was designed to address this gap. Funded by a grant from the Navy, it trains workers through an accelerated 16-week program with free housing and tuition. It recently entered its fourth year of operation, with a goal of helping meet the estimated need to add 100,000 workers to the submarine industrial base in the next 10 years.
The program was founded to bolster the Danville blue-collar machining workforce. Around 15 years ago, the city’s traditional industries slowly vacated the area, leaving the local economy in shambles until community leaders decided to invest in skilled trades workforce development.
The community has put more than $80 million into building “an incredibly sophisticated, robust and well-connected workforce pipeline,” Wells said.
Notable, however, is Danville’s landlocked location — about a three-and-a-half hour drive to the nearest shipyards in Norfolk, Virginia. The goal wasn’t to keep workers in the city; however, the constant influx of new students supports the community and provides a good pipeline for younger people growing up in Danville, Wells said.
“We’re bringing a lot of humans into our community, and we’re having to make sure they’re being taken care of, and the community is being taken care of, and each person comes from different backgrounds, different religions, different beliefs,” Wells said. “[With] all those dynamics going on, you learn a lot of lessons at a rapid rate.”
Danville’s machining pipeline starts at the sixth-grade level to spark interest. Participants can then hone their skills through high school programs, two-year programs, three-year programs and four-year degrees, and “there’s a very clear, well-connected path that allows them to get to that,” Wells said.
“That pipeline has had a high level of success in translating into skilled labor, and that has started to gain us recognition from other communities, from employers, from industry members,” he said.
The machining pipeline provided a foundation for the ATDM program, which was developed in partnership with the Institute for Advanced Learning and Research and Danville Community College. It attracted Navy and Defense Department interest in 2023.
Whitney Jones, deputy program manager for the Navy’s Maritime Industrial Base program, said ATDM provided an opportunity for the service to assume a “very proactive role” in the needs of the maritime defense industry.
“We’ve been part of everything from the planning and the strategic development to bringing the Navy, DoD and industry alongside this to understand the demand signal, to advocate for what this program offers our partners,” she said in an interview.
For the Navy, the program addresses a unique challenge for the shipbuilding defense industrial base: time to talent. Instead of waiting for potential workers to complete multi-year degrees or recruiting new graduates every summer, the Danville program provides the shipbuilding industry with new, well-trained employees about every four months.
“We have hiring demand now that’s not being met, and so ATDM provides a set of new entrants into our workforce or upskilled entrants into our workforce that have a much reduced time to talent,” Jones said. “ATDM is providing an opportunity for companies, shipbuilders, organizations to hire when they have the need, rather than on an annual cadence.”
About 55 percent of the program’s students are career-seekers, meaning they’re fresh out of high school or college and typically on the younger end. Twenty-five percent are veterans and retired military, while 20 percent are industry-sponsored, meaning they’re either established workers sent by their employers, or they were recently hired in the shipbuilding industry and do the training before starting work, Wells said.
Students can specialize in one of five program tracks: additive manufacturing; computer numerical control, or CNC, machining; quality control inspection, or metrology; welding; and non-destructive testing.
“All the paths are intertwined … essential core skill paths and skill functions that have been around; they’ve just basically evolved as technology has evolved,” he said.
Though the structure varies depending on the track, the program utilizes both classroom time and hands-on laboratory learning. The quality assurance and non-destructive testing tracks require more classroom hours because both are significantly more detail-focused and data-driven paths.
The additive manufacturing, CNC machining and welding tracks involve more time to learn how to operate their respective machines or tools.
On average, about 40 percent of the program hours are spent in a classroom, and the rest involve hands-on learning, Wells said.
In addition to training students with track-specific technical skills, the program dedicates a portion of time equipping students with soft skills, emphasizing training to be a functional part of a team in a manufacturing environment.
For example, the CNC machining students will make a component and deliver it to the quality assurance students, and if they find any deviations or defects, the instructors will coach them through communication and documentation of these issues and problem-solving.
“I feel like that’s a real differentiator that we try to build into this program to really make them industry-ready, beyond just being able to stand in front of a machine and make it do what it’s supposed to do,” Wells said. “The atmosphere and the environment [are] much more dynamic than that.”
The program’s instructors are integral to its success, Wells said. When the program first started, most of the instructors had been through the Danville machining pipeline themselves before working in industry.
To ensure the best instructors stay and enjoy working in Danville, the program pays them what they would make if they were still working in industry, Jones said.
“A CNC machinist in industry is going to make a whole lot more money in industry than they would in a classroom,” she said. “That provides consistency, it provides ‘best of.’”
The program also gives industry partners an opportunity to hire trained workers faster. Coordinating with over 200 partners, the program’s industry engagement team communicates with companies to see which ones are hiring and what needs they have, organizes job fairs and scours job boards to match students with partners.
Raymond Ryan, military and veteran recruiter at General Dynamics Electric Boat, said the program allows industry to “skip a step” in the hiring and training process.
“We can take people that don’t have any training … [and] when they apply and interview and get the job, they don’t have to do our eight, 10-week training,” Ryan said in an interview. “They’re going to go right into [on-the-job training] and start working. It’s a win-win for everybody.”
The program is currently in year four of its five-year ramp-up plan to reach full operational capacity of graduating 1,000 students and “pushing them back out into the industrial base,” Wells said.
As of January, 777 students had completed the training, and in 2024 it boasted a 90 percent placement rate for its graduates, recruiting from and placing students across 45 states, as well as Guam, Puerto Rico and Australia.
William Perry, an active-duty Coast Guard member and CNC machining student, said the program is an “awesome” opportunity to learn, especially on machinery “that I wouldn’t normally have access to, just such expensive equipment and nice equipment in such a clean environment and having such good instructors.”
Christopher Gardner, Navy veteran and quality assurance student, said the knowledge gained in the program is “incredible.”
“To give back to our country, that’s where you got to really get the big picture. It’s our defense system, and we need our country to build our defense system,” he said.
Going forward, ATDM and the Navy want to continue to ramp up the program by increasing student numbers and replicate the model in other parts of the country. Program leaders and service officials are currently discussing what that could look like, Wells said.
The Navy is already applying best practices learned from the program in other areas, such as funding a new maritime manufacturing program similar to ATDM in partnership with Macomb Community College in Michigan that focuses on training students in CNC machining and welding. The first cohort of 24 students started classes in late February.
As the program nears full operational capacity, ATDM must remain agile, proactive and prepared to anticipate shifts in the defense industry and the modern battlefield, Wells said.
“There are a lot of things that are starting to be introduced, like AI, that are going to have impact in manufacturing,” he said. “We have a responsibility to make sure we’re staying on that cutting edge … so we can ensure we’re giving our students and our industry partners the best opportunity to succeed in deploying those technologies, succeeding with those technologies and making sure that they’re staying competitive in a global market and a global landscape.” ND
Part 1: Navy, Industry Try to Reverse Course on Workforce WoesPart 2: Unions Say Retention, Not Hiring, Is Shipbuilders’ Biggest Problem
Part 4: Graybeards Spell Out Myths, True Fixes For U.S. Shipbuilding
Part 5: AI, Robotics May Attract New Generation of Shipyard Workers
Topics: Navy News